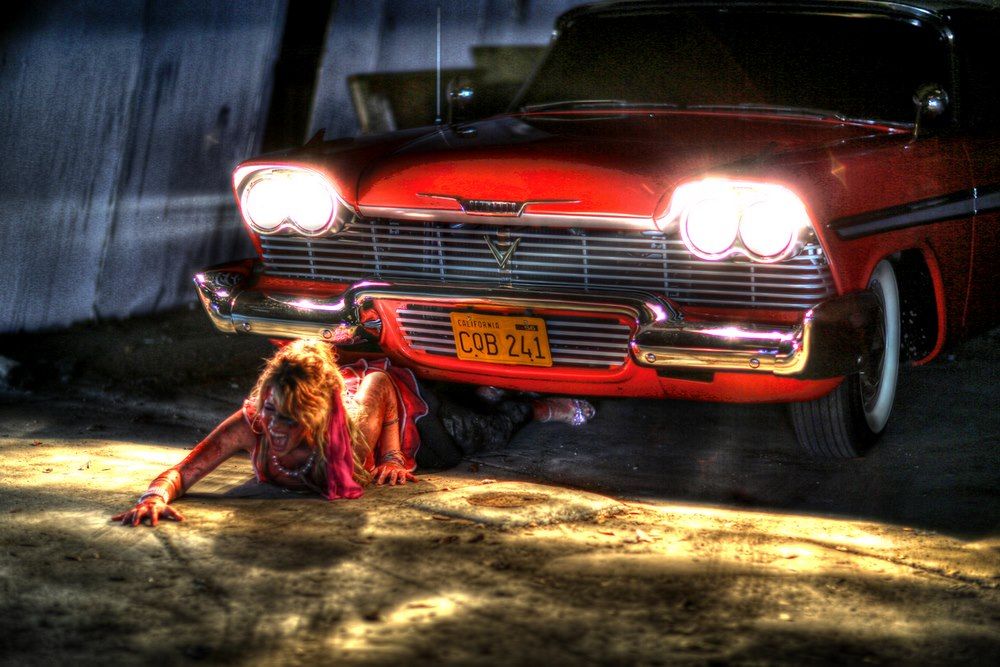
We translated this article by comrades from the collective Wildcat.
‘The state of the automotive industry is one of the most visible elements of a general crisis in industry.’
On the 20th of December 2024, VW’s works council and management agreed on an austerity programme that, among other things, would result in the elimination of 35,000 jobs by 2030 – most of the jobs will be cut in ‘too expensive’ factories in Germany. The production of the VW Golf is to be moved entirely to Mexico. Job cuts are also intensifying among suppliers, and are reaching machine and plant manufacturers (Kuka Augsburg).
Mercedes wants to double the share of production in low-wage countries from 15 to 30 per cent – in Kecskemét, Hungary, costs are claimed to be 70 per cent lower than in Germany. In 2023, an hour’s work in Hungary cost 12.80 Euros, compared to 41.80 in Germany. At nine per cent, corporate tax is lower than anywhere else in the EU. In addition, Orbán subsidises Audi, BMW and Volkswagen with hundreds of millions of Euros. The country is attracting people from Kazakhstan and Mongolia to counteract the shortage of labour and rising wages.
The ‘relocation strategy’ of recent decades has led to a standstill in innovation. German car companies no longer supply technology, but have to obtain battery know-how through new partnerships with Chinese companies. On top of the massive competition from Chinese carmakers, new tariffs and other trade barriers are now emerging. As an export-oriented country, Germany is becoming less and less suitable as a sales market – minus 27 per cent for electric cars in 2024. Even in the smaller United Kingdom, more electric cars were sold last year. Yet Germany is the second largest electric car producing country after China.
Even Tesla’s ‘innovations’ are increasingly turning out to be Musk’s ‘visions’ or even frauds. After each failure, he announces a new project to keep the stock bubble from bursting. That worked well for 20 years. Now he is trying to stop the rapidly collapsing sales figures and the foreseeable economic failure with a political coup. The US government has dropped an initial lawsuit against SpaceX. Further investigations by the US Securities and Exchange Commission and the Department of Justice against Musk’s companies are to be prevented by the shock of the mass layoffs in the civil authorities. But the ‘excessively strict regulations’, which Musk claims to be fighting against, often do not really exist (for example, in the case of fully autonomous driving in the US).
It could be a threat for Tesla (and others) that the Chinese carmaker BYD now wants to offer its assistance systems as part of the standard package. What costs several thousand dollars extra if you buy a Tesla would be included in the $9,500 BYD Seagull. If BYD’s move forces competitors to lower software prices – or to abandon paid subscription models altogether – the industry’s vision of raking in high profits through AI assistance systems will vanish into thin air.
The resistance to Musk is only just beginning. There are smaller protests happening outside of the factory floor. Under the slogan ‘Tesla Takedown,’ citizens are calling for a boycott in front of showrooms in major US cities. In view of the institutional coup by Trump/Musk and the massive job cuts across the automotive industry, mass strikes in Tesla, Volkswagen and Mercedes factories would be appropriate. But the employers’ rapid succession of blows – in Germany, but especially in the US – has left many workers in a state of shock. A brief wildcat strike by African lorry drivers in Germany in late January/early February was a small ray of hope (they were carrying loads including parts for the automotive industry) – but it shows that nothing has changed after Gräfenhausen [1] and the ‘Supply Chain Act’! [2]
When it comes to class politics, things don’t look any better for the Chinese competition: slave-like conditions and human rights violations. Most recently at the Serbian factory of the Chinese tyre company Linglong (which supplies VW) and during the conversion of a former Ford factory in Brazil that was bought by BYD.
Following a strike-happy 2023, the situation in early 2024 appeared to be as bleak as it is today,. However, more industrial disputes took place in Germany in the first half of 2024 than in previous years; at 171, there were more disputes than at any time since 2016. What’s more, the strikes lasted longer and were fought harder. In addition to wage increases, collective agreements and equal pay, workers increasingly demanded shorter working hours.
In the second half of 2024, the massive attacks by the car bosses began. Against this background, we published the following article in Wildcat 114. The editorial deadline was the 7th of December 2024.
from: Wildcat 114, Winter 2024
The auto and other crises
The ‘green transformation’ is failing and electric car sales are so low that the new car factories are making a loss. According to the coalition agreement of the ‘Ampel’ government (SPD, Green Party and the liberal FDP) in Germany, there should be 15 million electric cars on the roads by 2030. To achieve this, their share of new registrations would have to increase from 15 to 50 per cent with immediate effect – but it is falling. New ‘green jobs’ in industries are tending to decrease rather than increase. ‘Green’ start-ups are going broke. Northvolt, the flagship project of the European battery industry, has filed for bankruptcy. They can’t get the Chinese machines to work in the Swedish flagship factory.
In autumn 2024, hardly a week went by without new announcements of job cuts at all of Europe’s automotive companies and their suppliers. Bosch, Schaeffler, ZF, Magna, Continental and Thyssenkrupp are cutting tens of thousands of jobs and closing sites. Car production in Italy has collapsed, Ford has closed its factory in Saarlouis and is laying off staff in Cologne, and unemployment is soaring in the Austrian supply industry. At Volkswagen, the world’s second largest carmaker, management is overwhelming workers with bad news: in July, they announced the closure of the Audi plant in Brussels (after Audi bought the Sauber Formula 1 team in March for almost €700 million!). In September, they cancelled the ‘employment protection agreement’ introduced in 1994. This means that from July 2025, redundancies for operational reasons would be possible. The managers are demanding wage cuts of 10 per cent and want to close another three factories – this time in Germany, where VW employs 120,000 people.
As with the recent dockers‘ strikes in Hamburg, the media are supporting the employers’ attack with reports about overpaid workers and the usual references: will Wolfsburg become the new Detroit? Stuttgart the new Ruhr area? The employers are using the hullabaloo to torpedo the ‘Supply Chain Act’ as well. They are setting the agenda – and acting as if, after the closures and wage cuts, things will go back to business as usual, only with fewer workers.
Works councils and IG Metall have no alternative concept and are playing by the rules: they propose cost reductions of 1.5 billion Euros with wage restraint, flexibilisation of working hours and targeted job cuts. They are verbally radical at rallies and even organise token strikes (two hours per shift on the 2nd of December with 100,000 participants, four hours are planned for the 9th of December). The works council drivel about the ‘Volkswagen family’ is totally embarrassing. IG Metall can no longer play the role of moderniser as it did in the second half of the 20th century, because there is no longer any prospect of growth. Boosting car sales while lowering wages at the same time would only work if ‘consumers’ took out loans and got more into debt (as in the USA). Switching to the Chinese market no longer works either – quite the opposite!
The same systemic questions arise as in other industries – which products are socially desirable? How many? Who does the work? Who decides on investments? The difference is that the automotive industry is the key capitalist industry. The value added, the integration of completely different processes and workers, and the importance the automobile industry has for other sectors are greater than anywhere else. [3] The automotive industry combines mining and metallurgy (iron, steel, aluminium, etc.) with plant and tool construction, chemicals, electronics and transport. If you add road construction, service, etc., then no other industry depends on more jobs.
Cost reduction instead of conversion
Where car factories were built, a new stage of industrialisation and proletarisation began – and subsequently the struggles of car workers forced capital to develop: increase wages, hire people, automate. Many things still benefit us today: employee representation, collective agreements, safety and cleanliness standards at work, etc. But since the two ‘oil crises’ of 1973 and 1979, employers have no longer responded with ‘development’, but with globalisation and fragmentation of production. In doing so, they initially won on three counts: lower wages in newly industrialised areas, a boost in vehicle production due to the increased need for global transport, and fewer strikes due to smaller workforces. The price for this was a huge increase in environmental pollution and very complex global production and supply chains. Multinationals like VW, with over 100 factories and 600,000 employees worldwide, have emerged, along with thousands of suppliers and millions more workers. VW has to produce ten million cars a year to maintain the accumulated fixed capital and achieve the desired profit.
In 1972, the Club of Rome, which is partly financed by VW, formulated an ecological critique of mass motorisation – but it was directed against the workers’ struggles. VW itself did something completely different: it expanded. In the 1970s, VW was the first western carmaker to invest in China and the first foreign carmaker to open a factory in the USA. But by 1975, VW was in crisis, with the workforce to be reduced from 138,000 to 113,000. Most of the job cuts were handled by dishing out severance pay, with a few small departments being closed. [4]
At that time, the first plans were made – born out of the threat of factory closures – to convert production to ‘socially useful products’ (the famous ‘Lucas Plan’ in England in 1976; ‘conversion’ was discussed primarily after the First and Second World Wars and after the end of the confrontation between NATO and the Warsaw Pact).
A final lifeline for the car industry during its death throes came from social-democratic managers. They tried to reconcile ecology, technological development and profits, while ‘including’ the workers. For example, Edzard Reuter, CEO of Daimler-Benz AG from 1987-95, promoted an ‘open corporate culture’ that would ‘feel equally responsible to the capital providers, the workforce and the environment and act accordingly’. He wanted to turn Daimler into an ‘integrated technology group’. Similarly, Daniel Goeudevert, a French car manager and member of the Club of Rome, who sat on the board of management at VW from 1991-93 and was responsible for purchasing, advocated the expansion of public transport and the development of environmentally friendly cars.
Both Reuter and Goeudevert failed. With the ‘end of history’ came a 180-degree change in strategy during the sales crisis of the 1990s. At Mercedes, Reuter’s successor Jürgen Schrempp implemented ‘lean production’. At VW, Ignacio López, who remains to this day a notorious role model for all ‘cost-killer’ managers, introduced corresponding austerity programmes in the early 1990s. He had previously ruined Opel’s quality and reputation with his cost-cutting strategies; now he pushed through that VW suppliers would sell their parts for continuously falling purchase prices. This resulted in systematic quality defects, known in the industry today as the ‘López effect’.
VW introduced the 28.8-hour week in 1994, when the crisis was already over. IG Metall agreed to a wage cut and a massive intensification of labour. As a result, fewer workers had to build more cars in less time. Together with VW and the state of Lower Saxony, IG Metall founded its own temporary employment agency (GIZ), cancelled holidays of permanent employees etc. This was the basis of the ‘employment security agreement’, which was to last for 30 years. Volkswagen built up a foreign production network with the takeovers of Seat in Spain in 1988 and Škoda in the Czech Republic in 1991, as well as the factory in Bratislava in 1994, as a threat against workers in Germany (Bentley and Lamborghini were added in 1998, later MAN, Scania, Ducati and Bugatti).
Green capitalism?
To support car sales, the EU introduced emission standards from 1992 onwards. Stricter emission rules come into force roughly every four years. The carmakers were supposed to build cleaner engines bit by bit; consumers were supposed to be persuaded to buy new cars faster by issuing driving bans on their old ‘polluting’ cars. This stabilised sales, with new car sales rising by a few hundred thousand cars each year (EU-15 sales 1993: 10.9 million; 2003: 13.8 million). Since then, the old ‘polluters’ are no longer disposed of properly, but rather they are exported to Eastern Europe and Africa, where they pollute cities and increase the number of traffic deaths. [6]
The next corporate attack came at the turn of the millennium, again at VW. The then head of HR, Social Democrat and IGM member Peter Hartz, founded subsidiaries that hired workers at lower rates. Hartz introduced the concept of the ‘breathing company’, which ‘breathes in’ workers when the order book is full and ‘exhales’ them when it is empty. Together with the management consultancy McKinsey, VW’s own temporary employment agency AutoVision was created, later Auto 5000, another subsidiary, for whose workers the inferior ‘company wage agreement II’ applied. VW core workers saw the new ones as ‘cheap competition’; there was no joint struggle against this attack. Instead, works councils at individual VW plants organised workshops to increase productivity at their own location in order to attract investment and outdo their colleagues’ locations.
With the introduction of the euro in 2002, the competition that had already developed between workers in Western and Eastern Europe and within companies was further intensified. This happened because less productive countries could no longer avoid pressure by devaluing their currencies – thus, the low German unit wage costs were able to gradually take effect and the ‘German export model’ flourished. To do this, industry had to be able to access low wages. Once again, Peter Hartz came into play: in 2004, Hartz-IV [5] was introduced – a far-reaching benefit reform that increased the pressure to work and increased poverty. This created ‘one of the most modern low-wage sectors’ in Europe, as his friend and client Gerhard Schröder was pleased to note.
In 2005, Hartz was forced to resign after it was revealed that he had sent corrupt VW works council members to brothels and on luxury holidays at the company’s expense. However, neither this nor the wildcat strike at Opel in 2004 [7] could stop the general development: in 2006, a new collective agreement made working hours more flexible at VW and subsequently in the entire metal industry – the most important measure turned out to be that the number of hours that you could either have plus or minus in your annual working hours account was increased to 400. This made it possible to avoid mass layoffs when the crisis hit in 2009; short-time working did the rest – in the end, the German automotive multinationals weathered the global crisis without strikes. In 2009, there were only two publicly visible conflicts: a hunger strike by VW contract workers against their dismissal and a short wildcat strike by Daimler workers against the relocation of a car model.
In addition, the car industry was supported by state ‘scrappage schemes’. Consultancy firms called for a ‘downsizing’ of the industry, including plant closures, to reduce overcapacity and increase profit rates. The left wanted to hold a new ‘conversion’ discussion on how to overcome the destructive car system. The core workforces of VW and other multinationals had nothing to fear and did not fight against the former, nor did they care much about the latter. Due to a huge export boom to China, everything seemed to remain the same – ‘downsizing’ or ‘conversion’ was postponed.
China!
From 2012 to 2017, EU car production rose from 12.7 to 15 million per year, and employment in the German automotive industry rose from 742,000 to 834,000. In China, the rich, politicians and parts of the taxi industry bought the expensive cars from Germany. The ‘diesel scandal’ from 2015 (in which not only VW was involved) had no major impact on operating profits, but it did help a new criminal entrepreneur to succeed: Elon Musk, who used Tesla to give his anti-union mass production regime a greenwashing.
At certain points during that period, a third of the workers in German car factories were employed through temporary agency. Three quarters of the work to manufacture a car was taken over by suppliers who paid less than the main car companies – and who, in turn, outsourced work further. Labour costs in the new (subcontractor) factories from Poland to Ukraine, Serbia to North Africa remained low compared to German levels, despite some notable strikes. [8] In addition, there were moderate wage increases for the core work-force in Germany. These were the foundations of the successful export boom – and not, for example, innovation, superior technology or the like.
From 2019, sales and employment figures began to fall (except for Tesla). In 2020, the pandemic caused a brief slump, but the corporations had their wages subsidised through short-time work benefits again, they increased the prices of new cars – and made record profits. After 2022, the carmakers’ profit rates reached the next record in 2023, at an average of 8.6 per cent. The 16 largest carmakers rake in more than 150 billion Euros in profits per year. Mercedes, BMW and VW made several billion Euros in profits each year. Instead of Reuters’ ideas of acknowledging ‘employees and the environment’, the managers bribed the upper levels of the working class with money. Time and again, there were performance bonuses of several thousand Euros for German permanent employees. They paid high dividends to shareholders and awarded themselves 200 times the wage of a skilled worker.
The multinationals passed on a large part of the cost-cutting measures to suppliers by standardising the López method: we only guarantee you to buy parts from you if you guarantee us annual cost reductions. The suppliers that were large enough not to go broke cut jobs as a result. The nearly 100,000 jobs that have been cut in the German auto industry since 2019 were largely cut at the suppliers (a large share of the jobs at Opel were cut before 2019).
Some workers suffering from cost-cutting measures were able to attract attention by voting for the far-right AfD. [9]
The crisis…
Because of ‘China’, Germany was able to increase its absolute vehicle production slightly between 2000 and 2016 (in relative terms, as a share of global production, it was already falling). This ensured a little economic growth. The same applies to Spain and Eastern European countries. In France, Italy and England, on the other hand, vehicle production fell by more than half in each of these countries over the same period. [10]
Global car sales and production have been stagnating since 2017. Since then, production in Germany has also fallen. Almost two million fewer cars were produced in 2023 compared to 2016, in total four million. The ‘green transformation’, with a mix of billions in subsidies for electric cars and bans on combustion cars, should have boosted sales and thus production again – but in contrast to the introduction of the EU emissions standards in the 1990s, the electric car project went completely pear-shaped. The charging infrastructure is lacking, the range is still limited (and decreases even further in winter when you use the heating), ununderstood chemistry instead of logical mechanics, higher weight and more tyre abrasion (fine dust!) and an even greater dependence on software. In addition, German-made electric vehicles are far too expensive. Subsidies for industrial greenfield projects in the USA are higher and energy costs are lower. And above all, the competition from China is better.
From February 2023 to February 2024, industrial production in the Eurozone fell by 6.4 per cent, and in the EU by 5.4 per cent. German GDP is shrinking, and growth rates are struggling to get above 0.1 per cent. From January to September 2024, vehicle construction fell by 6.9 per cent compared to the same period last year. This is dragging down the mechanical engineering (minus 8.5) and electrical (minus 10.7 per cent) industries with it. Investments in new machinery are declining, foreign investments are at a record low, industrial companies are cutting thousands of jobs. The increasing arms production cannot even come close to compensating for this. The share of industry in GDP is declining.
China has changed from being the saviour of the German (car) industry to its potential gravedigger: Chinese companies not only have lower labour costs but also several years of technological headstart in the production of electric cars. Not only do they dominate battery production and machine / plant engineering, but the ‘smartphone-isation of the car’ also suits them. And just like Japanese car companies, they no longer rely on full automation; the share of personnel costs in Chinese car factories is 15 percent, in Germany 10 percent. They rely on engineers instead of financial honks and on creative ideas from colleagues for process optimisation. They have understood that innovations come from workers, not from machines. Permanent training under the slogan ‘lifelong learning’ amounts to eternal employee harassment. Chinese capitalists are doing what they have been doing for decades: they are copying and radicalising existing production methods – it is unlikely that they are not aware of the ‘López effect’ – nevertheless, on the 27th of November, BYD announced that it expects its suppliers to reduce costs by 10 per cent by 2025 in order to survive in the price war on the Chinese market. There, too, sales are stagnating, and manufacturers have to divide the cake among themselves. Many Chinese brands will go broke. The Chinese market is collapsing for German manufacturers. Also on the 27th of November, VW announced that it would close its forced labour factory in Xinjiang.
The state of the automotive industry is one of the most visible elements of a general crisis in industry and an expression of over-accumulation. As long as we are hypnotised by looking at falling sales numbers and hope for ‘green’ products, we won’t realise how general the crisis is. We are experiencing the implosion of cost-cutting strategies, management-by-stress and a corporate culture fixated on stock prices. The many expensive machine systems – no matter how highly digitised, artificially intelligent and networked – do not increase productivity and do not work for small-batch luxury production. As always, the employers are trying to use the crisis to restore the relationship between necessary and surplus labour in their favour. The form in which this is happening in Germany is ‘deindustrialisation’. Well-paid industrial jobs are being cut and rebuilt in new factories in low-cost countries: VW wants to invest in North America, BASF has built a second Ludwigshafen in China. In 2024, chemical production has fallen for the third year in a row and will be a fifth lower than before the pandemic.
Germany and its supplier states in Central Europe are in the midst of a massive industrial crisis. The German export model, which has long been responsible for growth and a higher standard of living than elsewhere, is at an end. We are in the middle of the long-delayed attack on core workforces. The deindustrialisation is intended to wear them down, the crisis scenario is intended to shock everyone and clear the way for a new labour regime. In addition to the ‘employment security agreement’, VW has also terminated other collective contracts: for better pay for temporary workers and one for the takeover of apprentices. An agreement that regulates the co-management by the works council regarding pay and conditions in excess of those determined by the general collective contract is likely to be scrapped. As in the 1990s and 2000s, management is playing off old against young, office against assembly line and production locations against each other….
… is an opportunity
In the third quarter of 2024, VW, Mercedes and BMW together spent 8.7 billion Euros on research and development – and despite this were able to record an operating profit of 7.1 billion. The diesel scandal will have cost Volkswagen an estimated 32 billion Euros. With more than 150 billion Euros in debt, VW is one of the three most indebted companies in the world. Nevertheless, VW’s 2023 balance sheet shows a net profit of over 16 billion Euros. Of this, 4.5 billion was distributed, almost half of it to the Porsche-Piëch clan. Those who read not only the VW press releases but also the balance sheets will find ‘no further ammunition for the management’s argument that historic cost reductions and sacrifices must be made by the workforce in Germany’ (Bernstein Research). The bosses do not have to avoid losses, they want higher profits! [12]
In a situation of plant closures, workers’ power seems to disappear at first. Works councils and climate activists propose self-management and “meaningful production”, for example trams, trains, buses, bicycles. Many see the mobilisation at GKN in Italy as a model, young people discuss the compatibility of ecology and production. In northern Germany, activists are also targeting Tesla and VW, some are making existential decisions (activists moved to Wolfsburg and propagated a fundamental change in the transport sector: VW should build public transport; however, the first attempt failed). The discussion among left-wing activists is at the stage where it is agreed that the industrial capacities – plants and workers – are needed by society. [13] But so far, self-managed companies have quickly fallen by the wayside in the face of competition. Besides, there is also overcapacity in train, bus and bicycle factories. Others propagate the fight for maximum severance pay – let the place close and at least make the employer pay dearly. Deindustrialisation and a ‘structural change’ towards a ‘service economy’ mean lower and more unequal wages. Without industry, the proletariat becomes impoverished, as can be seen in the USA, Italy, etc. It is therefore of some significance whether the (VW) core workforce continues to merely watch their official representatives assist the capitalist fools, or whether they overcome their state of shock.
On the 30th of November, it was announced that Audi had sold a third of its Formula One shares to the Qatar Investment Authority.
On the 2nd of December, Carlos Tavares, the long-standing Citroën, Fiat, Opel restructurer and Stellantis boss, who was in the tradition of López, was dismissed more quickly than planned. To everyone’s surprise, his cost-cutting programmes turned out to be ‘unsustainable’.
On the 5th of December, the conservative EPP fraction of the European Parliament issued a position paper in which it proposed to reverse the combustion engine phase-out and to postpone new CO2 fleet limits (average amount of CO2 pollution of the total model range of a car maker). If the car giants had to pay penalties for not meeting the limits, the money should not go into the EU budget, but back into the car industry. Brilliant!
Footnotes
[1] Graefenhausen: In 2023 truck drivers, primarily from Georgia and Uzbekistan, occupied a service station in Germany for ten weeks in order to protest against not having been paid their outstanding wages by the transport company from Poland. Our article here
[2] ‘Lieferkettengesetz’: This law was enacted in 2024 and stipulates that companies in Germany with over 1,000 employees have to take legal responsibility for what is happening in their global supply chains.
[3] ‘The gross value added by a job in the automotive industry is 2.5 times higher than for an average job. Even if everyone who loses a job in the automotive industry immediately finds a new, average job, we still lose six per cent of our prosperity.’ (Sebastian Dullien) ‘Gross value added is the difference between the total value of goods and services produced and the value of inputs, i.e. the costs incurred in the production process.’ Kathrin Werner: Deutschland ohne Autoindustrie – wie groß wäre der Schaden? [Germany without a car industry – how bad would the damage be?] Süddeutsche 12.11.2024.
[4] Christian Müßgens: Volkswagens Urkrise [Volkswagen’s original crisis], FAZ 23.11.2024.
[5] Haiko Prengel: Ab nach Afrika [Off to Africa], Süddeutsche 8.3.2021.
[6] Wildcat article on the Hartz4 reform protests: https://libcom.org/article/protests-against-welfare-reform-germany-2004
[7] Wildcat article on the Opel strike: https://libcom.org/article/one-week-wildcat-strike-general-motorsopel-bochum-2004
[8] In the dossier ‘Auto’ on our website you will find ‘auto articles’ for each phase, for each strike, etc.
[9] ‘In Thuringia, the AfD received 49 percent of the votes from workers, in Brandenburg 46 percent, and in Saxony 45 percent of the workers. The influence of the far right obviously extends deep into the trade unions. According to the Konrad Adenauer Foundation, 42 per cent of unionised blue-collar workers and 30 per cent of unionised white-collar workers voted for the AfD in Thuringia. Klaus Dörre: Die verlorene Ehre der Arbeiter, bpb.de 20.11.2024
[10] Comprehensive data is provided in an IW Report from 22 September 2024: Thomas Puls: Die Automobilindustrie im Jahr 2024 [The Automotive Industry in 2024], IW Report 38/2024
[11] See Wildcat 113: What Energy Transition? The Electric Car and the Return of Mining, late summer 2024: https://www.angryworkers.org/2024/10/27/what-energy-transition-wildcat-on-the-current-global-moment/
[12] See: Stephan Krull: Autoindustrie: Abstiegsängste und Abwehrkämpfe, Z 140, 24 November 2024. And: Autoindustrie – Abbau oder Umbau?, nd, 6.12.2024.
And: Suitbert Cechura: Konzept für Entlassungen, Junge Welt 5.12.2024.
[13] Jürgen Bönig: Nachhaltig zerstören – geht die Automobilindustrie den Weg der Druckmaschinenhersteller? [Sustainable destruction – is the automotive industry following the path of printing press manufacturers?] Lunapark 21, Winter 2024 – In 1961, Raniero Panzieri showed that there can be no technological continuity after the revolution because capitalist production relations are inherent in the productive forces. See: https://libcom.org/library/capalist-use-machinery-raniero-panzieri